CNC Machining: The Cornerstone of Automotive Performance Parts
The automotive industry extention prompts automakers seeking for precision, efficiency, and innovation automotive components, especially when it comes to performance components. These creative components are integral to enhancing vehicle performance, durability, and safety. Among the advanced manufacturing techniques available today, People find that Computer Numerical Control (CNC) machining stands out as a critical process for producing high-quality automotive performance parts. This article explores why CNC machining is the cornerstone for Automotive Performance Parts.
1. Precision and Consistency
As Automotive performance parts, they require exact specifications to function optimally. Whether it’s turbochargers, cylinder heads, or suspension components, even minor deviations can affect a vehicle’s overall performance.
CNC machining offers unparalleled precision through computer-controlled tools. It ensures dimensional accuracy within microns. Also this precision translates into improved engine efficiency, reduced friction, and better durability for high-stress components.
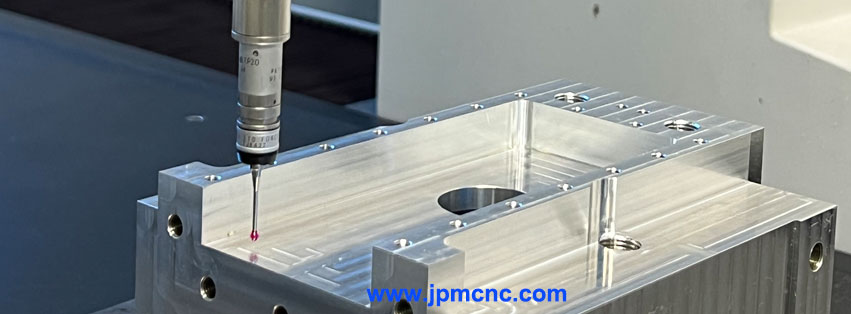
precision machined components
2. Compatibility with Complex Designs
The automotive performance parts need more complex and multi-functions design structures. Modern performance parts often feature intricate geometries, undercuts, and tight tolerances that are impossible to achieve with traditional machining.
However CNC machining creates such complex designs. With multi-axis machines, manufacturers can produce these specific parts with detailed contours, intricate patterns, and seamless finishes. Advanced cnc machining equipment can lightweight yet robust components for enhancing speed and fuel efficiency in automobiles.
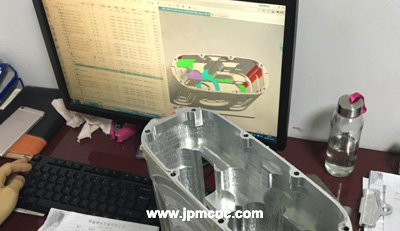
CNC machined Aluminum camera parts and thermal imager components
3. Material Versatility
Performance parts must endure extreme conditions, including high temperatures, pressure, and wear. So these performance parts can be made of reliable material. CNC machining allows a wide range of materials, from lightweight aluminum alloys to high-strength titanium and steel.
For instance, aluminum CNC machining is widely used to create lightweight components like intake manifolds, while titanium is ideal for heat-resistant parts such as exhaust systems. The flexibility to work with diverse materials makes CNC machining processes more suitable automotive performance parts.
4. Enhanced Prototyping and Customization
The automaker often requires rapid prototyping parts to test designs before mass production. CNC machining enables quick and accurate prototyping, allowing engineers to iterate and refine designs efficiently. The Rapid CNC Machining Services should be provided by the professional cnc machining manufacturer.
Moreover, CNC machining supports customization for induvidual automotive performance parts. Enthusiasts and racing teams often require bespoke solutions tailored to specific vehicles or racing conditions. CNC machining can produce custom parts without compromising quality or delivery timelines.
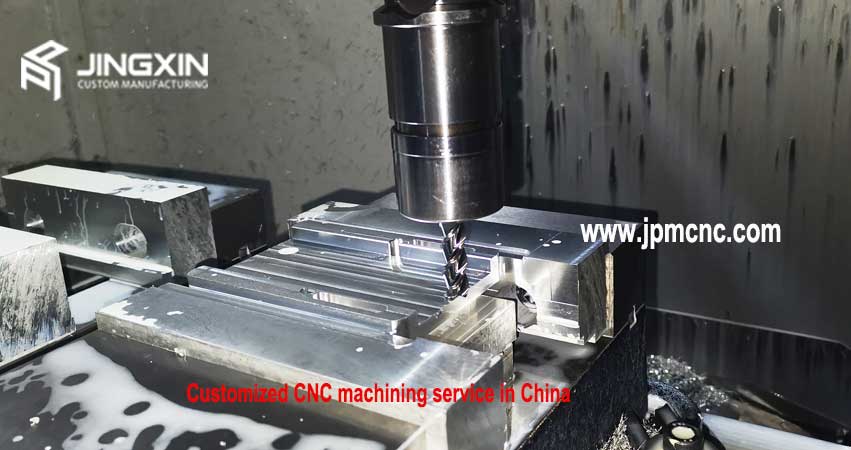
Custom CNC machining services china auto jigs supplier
5. Cost-Effectiveness in Long-Term Production
While the initial setup cost of CNC machining may seem high, its efficiency and automation result in lower labor costs and reduced waste. This cost-effectiveness is especially significant for high-performance automotive parts, Its process is high precision, and machined parts is produced by cnc machining is practice and durable. Their long time applications shows the character of cost-effectiveness.
Additionally, CNC machining’s ability to operate continuously with minimal supervision ensures consistent output, making it ideal for both small-batch and mass production.
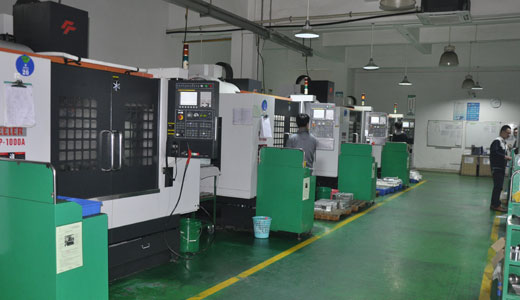
CNC machine shop China,Precision CNC machined parts supplier
6. Improved Surface Finish and Durability
Some performance parts, especially for components exposed to high friction or aerodynamic forces. CNC machining provides superior surface finishes, because this process have a tight tolerance dimension and create a even smooth surface finish.
High-quality finishes also contribute to part durability by minimizing stress concentrations and improving wear resistance. This ensures that performance parts maintain their integrity over extended periods of use.
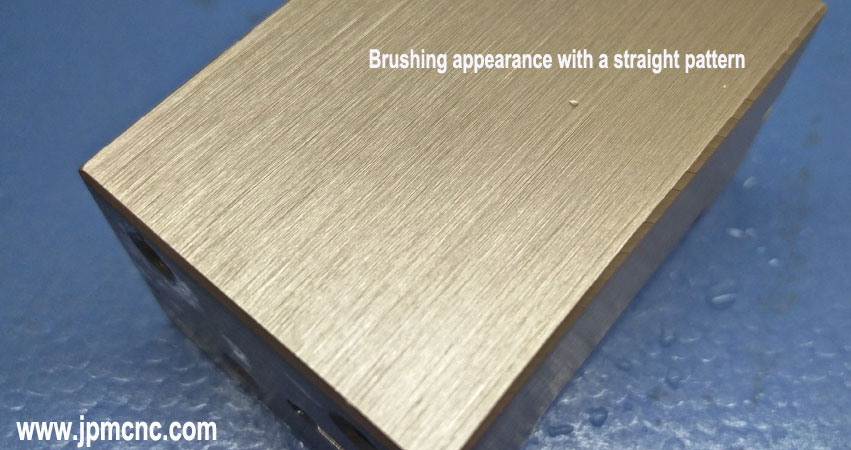
CNC Machined Parts Finishing,Tips of Tips of Surface Finishing For CNC Machined Parts
Conclusion
CNC machining has optimized continuously the production of automotive performance parts by offering precision, versatility, and efficiency. It can handle complex designs, support diverse materials, and deliver cost-effective solutions. This makes it an essential technology in the automotive industry. This is just the real reason that CNC Machining is Essential for Automotive Performance Parts.
For manufacturers, adopting CNC machining not only enhances the quality of their products but also positions them as leaders in a competitive market. As the demand for high-performance vehicles continues to grow, CNC machining will remain lead sheep in the quest for innovation and excellence.
CNC Machining’s Applications in the Automotive Industry
CNC (Computer Numerical Control) Machining is Essential for Automotive Performance Parts, supporting the production of complex, high-performance, and reliable and durable components. By offering precision, scalability, and versatility, CNC machining had been used in nearly every aspect of vehicle design and manufacturing. We will explores the critical roles CNC machining plays in the automotive sector and highlights its stand out in advancing modern vehicle technology.
1. Engine Components
CNC machining is indispensable for producing engine parts that require tight tolerances and high durability to withstand extreme conditions,such as heat resistance, corrosion resistance. The process methods include of cnc machining, cnc milling, cnc turning and cnc drilling and tapping etc. These components include of the follow items:
- Cylinder Heads and Blocks: Machining ensures proper alignment of chambers and ports for optimal airflow and combustion efficiency.
- Pistons: CNC machining creates lightweight yet strong pistons for improved engine performance and reduced fuel consumption.
- Camshafts and Crankshafts: Precision machining guarantees smooth surfaces and accurate profiles, reducing friction and wear for improved longevity.
2. Transmission Systems
Transmission components require intricate designs and robust construction to handle torque and power transfer efficiently. CNC machining enables:
- Gear Manufacturing: Producing gears with precise teeth profiles to ensure seamless power transmission and minimal vibration, and produces a high effective drive power.
- Clutch and Differential Housings: Automobile need Lightweight but durable housings made from materials like aluminum and titanium are achieved through CNC processes and ensure having a fuel efficiency and energy power conservation. Some custom aluminum components need be processed by precision cnc machining equipment. These components are critical for achieving smooth driving dynamics and performance.
3. Suspension and Steering Systems
Automobile Safety and comfort heavily rely on the suspension and steering systems, which consist of CNC-machined components such as:
- Control Arms and Knuckles: High-strength parts machined to withstand dynamic forces during operation.
- Steering Racks and Linkages: Precision components for responsive and accurate vehicle handling.
4. Brake Systems
CNC machining plays a pivotal role in manufacturing braking components that prioritize safety and performance.
- Brake Calipers: In Automotive brake systems, There is a little crack between brake caliper and rotor, So Machined for strength and precision to ensure even clamping pressure on brake pads.
- Brake Rotors: They need a tight flatness and more friction when braking. However CNC Machining processes provide smooth, balanced rotors that minimize vibration and offers consistent braking performance.
- Hydraulic Cylinders: Precisely machined to ensure proper fluid dynamics and reliability in hydraulic brake systems.
5. Lightweight Body Components
As the industry transfers toward electric vehicles (EVs) and fuel-efficient designs, lightweighting has become a top priority. CNC machining can create high quality structural and aesthetic parts, such as:
- Chassis Components: In order to reducing overall weight of EV, adopting Machined aluminum and magnesium alloys provide strength without added weight.
- Aerodynamic Features: Custom air vents, diffusers, and spoilers enhance vehicle performance and aesthetics.
6. Electric Vehicle (EV) Components
The rise of EVs has introduced new challenges for automotive manufacturing, many of which CNC machining addresses effectively:
- Battery Enclosures: CNC machining creates lightweight, heat-resistant housings for EV battery packs.
- Motor Housings: Precision machining ensures alignment and balance for efficient electric motors.
- Cooling Systems: Machined components like heat sinks and fluid channels are critical for thermal management in EVs.
7. Prototyping and Customization
Innovation in the automotive industry depends on the ability to test and refine new designs. CNC machining is widely used for:
- Rapid Prototyping: Quickly producing test components to validate designs before mass production.
- Aftermarket Customization: Creating bespoke parts for performance upgrades, such as custom intake manifolds, exhaust systems, and suspension parts.
8. Interior and Trim Components
Beyond functional parts, CNC machining also contributes to interior aesthetics and comfort:
- Dashboard and Control Panels: Machined from metals, plastics, or composites for a premium look and feel.
- Knobs and Handles: Precision-machined aluminum or steel components add durability and elegance to vehicle interiors.
- Decorative Trim: Custom-machined accents enhance the luxury and personalization of vehicles.
9. Safety Systems
Safety-critical systems, such as airbag components and seat belt mechanisms, rely on CNC machining for precise and reliable parts. For example:
- Airbag Housing and Deployment Mechanisms: These components are cast mostly by zinc and aluminum alloy. With CNC machining to process them and ensures structural integrity and precision in triggering systems.
- Seatbelt Anchors: These performance components are processed by cnc machining to meet high strength standards for passenger safety.
10. Autonomous and Connected Vehicles
The shift toward autonomous and connected vehicles introduces new requirements for precision parts, such as:
- Lidar and Radar Housings: CNC machining ensures accurate alignment and protection for advanced sensors.
- Electronic Components: Heat-resistant housings for chips and processors critical to autonomous systems.
From the above several points, We found CNC Machining is indispensable process in the production of automotive performance parts. In automotive sectors, whenever fuel-efficiency automobiles or electric vehicles, cnc machining can all produce high performance functional components to innovate newly cars and vehicles. Rely on the precise and tight tolerance accuracy of cnc machining, automotive parts manufacturer can provide high quality and qualified standard components to automakers. As CNC Machining: The Cornerstone of Automotive Performance Parts.
Conclusion
CNC machining will optimize continouesly automotive manufacturing, and improve consistently the production of precise, durable, and innovative components. Its applications involve of every facet of vehicle design, from powertrains to interiors. With rising of Electric vehicles, CNC Machining transfers to some innovation automotive performance parts process like electric sensors and smart devices.
For automotive parts manufacturers, investing in CNC machining capabilities is not just a choice but a necessity to remain competitive in a rapidly evolving market. By leveraging CNC technology, they can ensure quality, efficiency, and innovation automotive performance parts. CNC Machining: The Cornerstone of Automotive Performance Parts.