There is a dimension tolerances in CNC manchining during processing a part, the tolerances can meet the requirements of smooth installment and usage functionality of the part. Different material, precision tolerances is different, responses different process requirements. Whenever, the tolerances should have a range, no fixed figure. Avoid dead result. Today we delt into tolerances in cnc machining in detail and how to inspect and test the tolerances to achieve client’s requirements.
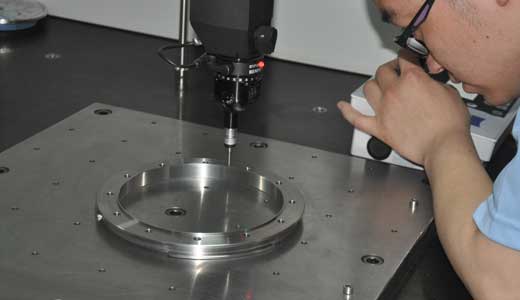
tight tolerance precision machined products, 3D CMM specturm testing instrument
What Is Tolerances in CNC Machining ?
Tolerances in CNC machining means the allowable variation in a part’s dimensions while complying with the design specifications. These tolerances are crucial because they decide the precision and functionality of the machined component. More tighter the tolerance, more closer the final product must be to the specified dimensions, and this can significantly impact the manufacturing process, cost, and overall quality. But also the tolerances in cnc machining are rigidly made out from practical installments and cnc machining technique.
Types of Tolerances in CNC Machining
From types of cnc machining processes, classified into the follow items.
Linear Tolerances
Control the allowable variation in straight-line dimensions, such as length, width, and height. These dimensions of the machined component can be measured by Two dimensions instruments, Caliper and micrometer and controlled in effective.
Geometric Tolerances
Define permissible deviations in shape, orientation, and location, including flatness, roundness, and parallelism. These dimensions can be observed by projector and have a precision accuracy handling.
Angular Tolerances
Specify allowable deviations in angles between features. This is essential to manufacturing injection molding tools. Angular tolerances determine whether the injected part stuck the mold and ejecting pin ejects the part out of the mold smoothly. Coordinate Measuring Machines (CMMs) are used to measure the precision angular tolerances.
Fit Tolerances
Ensure proper assembly and interaction between parts, These tolerances evenly come from our practical assembly and installment technique. It standard is object to have smooth running after installing these machined parts together.
Common Tolerance Ranges
As precision machining manufacturer,who are known that Typical CNC machining tolerances range from ±0.005 inches (±0.13 mm) to ±0.0001 inches (±0.0025 mm), depending on the machine capabilities, material properties, and design standard. Includes of the follow types.
Standard Tolerances: Suitable for non-critical parts or prototyping. It implements common default standard tolerance.
Tight Tolerances: Necessary for high-precision applications like aerospace, medical, or automotive components.They need precision dimensions so that these parts can be fit and smooth each other. Moreover realizing their functionality in precision equipment.
Factors Affecting Tolerances In CNC Machining
From the below aspects, we summarize key points from our practical working and components machined assembly.
- Material Selection: Different materials should correspond different machining processes. Metals like aluminum and steel are easier to achieve tight tolerances compared to softer or more elastic materials like plastics. More higher hardness material , more tight tolerances precision.
- Tooling and Machine Capabilities: Modern CNC machines can achieve tighter tolerances, but this depends on their accuracy, stability, and maintenance. From three axis machines to five axis machines, they will have different process capabilities and precision tolerances. Which machine is suitable for your parts, depends on parts functionality and durability completely.
- Environmental Conditions: Factors like temperature and humidity can cause material expansion or contraction, impacting tolerances. Some machined components need standard tolerance only, but it must be strong corrosion resistance and wear resistance. So the component can be made of zinc or aluminum material,that is enough. However mechanical components in aerospace and telecommunication, which need running smooth, without any factors, Certainly these components may be made of high speed and stainless steel material.
- Design Complexity: Intricate geometries may require looser tolerances to accommodate the limitations of the machining process. These parts is possible meeting aesthetics and decoration of being attractive to eyes’ball, with less dimensions tight tolerances.
Ensuring High-Quality, High-Precision Products In CNC Machining
How to ensure machined products high quality and high precision in CNC Machining ? Meeting the follow terms is so crucial for cnc machining manufacturers. Please regard the guideline as your best reference.
-
Design for Manufacturability (DFM)
Collaborate with engineers to define tolerances that balance functionality, manufacturability, and cost. Avoid unnecessarily tight tolerances unless absolutely required by the application.
-
Precision Machines and Tools
Use high-quality, well-maintained CNC machines. Invest in cutting tools with minimal wear to ensure dimensional accuracy. Three axis CNC Machining Center and Five Axis CNC Machining center is considerable available.
-
Material Handling
We should choose qualified material in accordance with functionality of machined part. Select materials with predictable machining properties as soon as possible. Account for material stress relief and thermal stability during machining.
-
Inspection and Quality Control
Adopting advanced metrology tools, such as Coordinate Measuring Machines (CMMs), laser scanners, and optical comparators. Perform regular inspections during and after machining to detect and correct deviations early.
-
Skilled Workforce
Hire experienced machinists and engineers who understand the importance of tolerances.Provide continuous training machining technique and production management and ensuring products quality .
Attention Points for Tolerance Management
- Communicate Specifications Clearly: Making a statement that tolerances are explicitly in the technical drawings and CAD models.This is what client should present to supplier before drawing and design visual models so that cnc machining manufacturer can understand what is client means in deed.
- Consider Assembly Requirements: Apply fit tolerances that account for how parts will interact in the final assembly. CNC machining manufacturer ask the client to offer all setting unit to test fit assembly in during and after machining and avoid some uneccessary defects occurred.
- Balance Tolerances and Cost: Tighter tolerances often mean higher costs, This is due to slower machining speeds, increased tool wear, and additional inspection steps. CNC manufacturer should predict that possible issues occurred in cnc machining and notice their clients and negotiate the quotation with their customers and balance tolerances and cost of machined parts. Caculating the best price to their client.
- Plan for Post-Machining Processes: Some machined parts may be done secondary operations like polishing, anodizing, or heat treatment, which may slightly alter dimensions. Once the functionality of part can achieve client’ requirements, we should do all.
Conclusion
Understanding Tolerances in CNC machining can ensure high quality and high precision machined components. It involves of several factors impact. Includes of material selection, advanced machinery, skilled craftsmanship, and rigorous quality control, manufacturers can consistently produce high-precision components that meet or exceed customer expectations.