3 Major 3d printing processes and technology introduction
After several decades of development in 3d printing technology, Now there are a variety of 3D printing technology process. From the categories,It is divided into extrusion molding, granular material molding, photopolymerization and other moldings.
The mail technique includes Fused deposition modeling(FDM), Electron Beam Melting(EBM), Selective laser sintering (SLS), 3D platform (3DP), selective heat sintering (SHS), Stereolithography Apparatus(SLA), digital light projector (DLP), etc. 3d printer works with 3D STL file. Fused deposition modeling(FDM), Stereolithography Apparatus(SLA) and Selective laser sintering (SLS) are 3 major 3d printing processes in present applications.
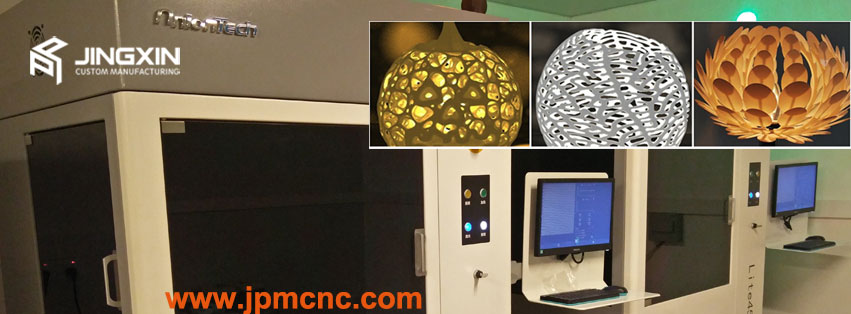
SLA Rapid prototyping services,3 Major 3D printing technology introduction
3d printing is advanced technology for rapid prototyping
FDM, SLA, SLS as the mail advanced technology. Fused deposition modeling(FDM) 3D printing generally works with thermoplastic materials to filament form for the material. The material is heated and melted in the nozzle, the nozzle along the part of the profile and fill the trajectory movement. While the molten material extrusion, the material quickly solidified, and with the surrounding material condensation.
Stereolithography Apparatus(SLA) also known as stereolithography, light Forming, etc. It is a rapid prototyping process that uses a laser beam to scan a liquid photosensitive resin by point-by-step scanning.
Selective laser sintering SLS process, is the use of the infrared laser as a heat source to sinter the powder material, and layer by layer forming three-dimensional parts of a rapid prototyping technology.
3DP process and SLS process similar to the use of powder Material forming, such as ceramic powder, metal powder. The difference is that the material powder is not connected by sintering. But through the nozzle with the adhesive part of the part of the “printed” on the material powder above.
Fused deposition modeling(FDM)
1.Overview
FDM is the abbreviated form of “Fused Deposition Modeling”. To understand FDM molding technology, first of all, we need to change thinking. Usually, 2D printing is done on a sheet of paper (one plane), however 3D printing is done to print a three-dimensional model. .FDM melt deposition is a one of kind melt deposition 3D printing technology. In terms of operation is to use the high-temperature materials that will be melt into liquid. Through the print head after extrusion, and finally in the three-dimensional space arranged to form three-dimensional objects.
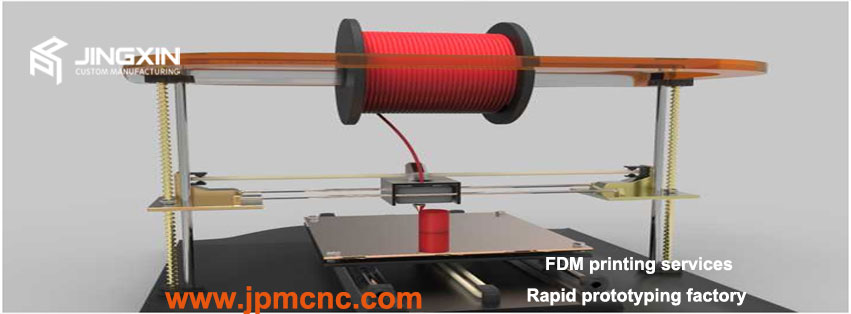
FDM 3d printer used for rapid prototyping services
FDM molding technology mainly relies on the print head and print platform to achieve the three-dimensional model of the building. Throughout the 3D printing process, the wire plays a vital role in the composition of the entire print model. FDM 3D printers have a wide range of applications. They are constantly breaking through their own limits and achieving more possibilities in more areas.
2.FDM history
Starting with the historical origin of the melt deposition molding technology. FDM technology appeared in the late 1980s. In 1988, S. Scott Crump invented the FDM (Fused deposition molding), the following year S. Scott Crump established Stratasys company. In 1992, the first FDM 3D printer was sold out.
3.FDM operation
Among all 3D printing technology, FDM printer’s mechanical structure is the most simple. The design is also the easiest, manufacturing costs, maintenance costs and material costs are the lowest. It is most popular 3D printing technology used for desktop 3D printer and industrial FDM machines.
The principle of FDM process is as follows. The heating nozzle is under the control of the computer. According to 3D STL file of the product profile information, X, Y plane movement, thermoplastic filament material from the wire feeding mechanism sent to the hot nozzle. In the nozzle heating and melting into Semi-liquid, and then squeezed out, selectively coated on the table. The rapid cooling to form a layer of about 0.127mm thickness sheet outline. A layer of the cross-section of products is finished. Then a certain height of the table would be down and then the next layer would be printed by layer by layer. The final formation of three-dimensional product parts would be created as you designed on the computer.
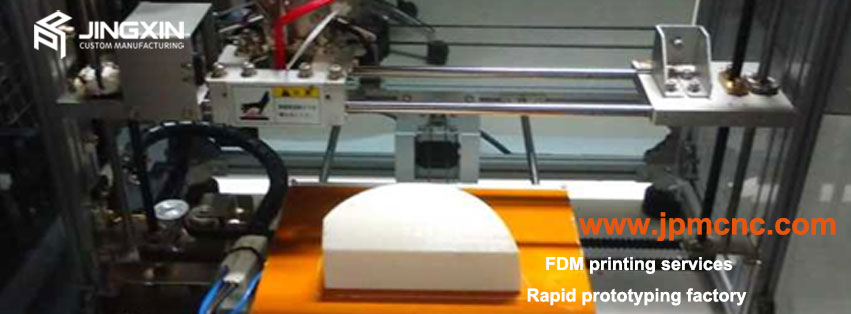
FDM Rapid prototyping services,3D prototyping services, SLA 3D PRINTING
4.Material for FDM printing
FDM 3D printed products are layered after the hot melt. The most common of FDM molding raw wire material is ABS and PLA basing on the type of wire. With the increase in 3D print products and the progress of 3D printing technology, supplies, 3D printer manufacturers continue to develop the various material that can be used for FDM 3D printing. Recently a metal like printing wire and also a hardness higher than the previous PLA HS wire was born. FDM has a lot of wire, such as ABS, PLA, nylon, wood, and even food. Over time, more and more 3D printer manufacturers began to join the wire production. Compared to general-purpose wire manufacturers, 3D printer manufacturers introduced wire more suitable for the manufacturer’s 3D printers. Most of the wire in the diameter of 1.75mm, 3.0mm.
5.FDM Application
FDM has its unique advantages over traditional production methods such as Rapid CNC prototyping, Vacuum casting. First, you can create more precision mechanical parts. Second, Low cost for mass production made by FDM process. By the price is getting lower and lower, printing costs are getting lower and lower. Thus FDM 3D printers are increasingly accepted by consumers.
6.FDM Advantages & Disadvantages:
Advantages: high precision, hardness is good, a variety of colors.
Disadvantages: rough surface on printed parts.
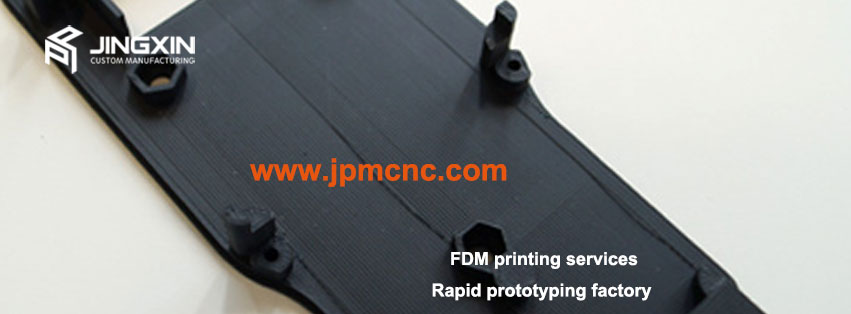
FDM 3d printing services, SLA prototype service, rapid prototypes
FDM technology has the advantages of Rapid manufacturing and low cost. But the, it is difficult for desktop FDM printer to accurately control the appearance and molding affection. Since desktop FDM printer’s discharge structure is simple. Meanwhile the temperature for the FDM molding effect is very large. The desktop FDM 3D printer Usually the lack of constant temperature equipment, so the tolerance of parts is up to usually 0.3mm-0.1mm. In addition, most of the FDM models produced the edge of the product has a layered deposition of the “step effect”. You can clearly see the layered stack and a ray of strands of support lines, so FDM printer is not recommended for the parts or rapid prototyping with high precision and good surface requirements.
Stereolithography Apparatus(SLA)
1.Overview and process
Light curing technology is the earliest developed rapid prototyping technology. It is currently the most in-depth, the most mature technology. The most widely used one of the rapid prototyping technology. Light curing technology, the main use of photosensitive resin as the material. Through the ultraviolet light or other light source solidification molding, layer by layer curing, and ultimately get a complete product.
The advantages of light curing technology are that the molding speed is high, the prototype is high precision. It is very suitable for the production of high precision and complicated structure parts. The use of light-curing technology for industrial-grade 3D printers, the most famous SLA 3D printer manufacturer is the Objet. They also offer more than 123 kinds of photographic materials. It is currently the most supportive material for 3D printing equipment.
2.SLA 3D Printer Main Object Material Classification
The objet offers material with minimum layer thickness can reach 16 microns (0.016 mm).
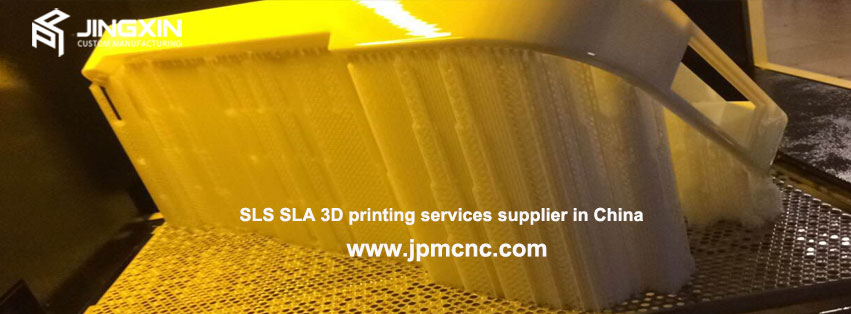
SLA-3d-printing-services
3.SLA Advantages & Disadvantages:
SLA Advantages
- SLA is the first process that is used for SLA rapid prototyping process.
- Directly made from CAD digital model prototype, high processing speed, quick turn and short lead time, no cost for tooling and molds.
- You can process prototypes and molds that are structurally complex or difficult to form using traditional means.
- Visualize the CAD digital model to reduce the cost of design modification.
- Provide samples for the engineering testing and verify the design by real parts to reduce the risk of by computer solution.
- Can be operated online and the facilitates can be remotely controlled as production automation. Low labor cost.
- Compared to other 3D printing processes (such as FDM) of hot melt materials, SLA has high molding accuracy and smooth surface.
SLA Disadvantages:
But SLA 3d printing process has two shortcomings, first, the photosensitive resin raw materials have some toxicity, the operator needs to pay attention to protection.
4.SLA 3D Application
SLA Applications include almost all areas of manufacturing and rapid SLA 3D printing prototype services. Such as the medical, ergonomic, cultural relics protection and other industries have also been more and more widely used. At present, it is mainly used in the design verification of new product development and the pre-production of new products. That is, from the concept of product design → design → structural design → basic function evaluation → simulation sample trial development process. For some of the plastic structure of the main products can also be a small batch production. Or some physical aspects of functional testing, assembly verification, the appearance.
- Cars, motorcycles: Checking the design and assembly test for engine and cylinder head.etc
- House Appliances: appearance and structure design of various home appliances, assembly test and functional verification, marketing, mold manufacturing.
- Communication products: product shape and structure design, assembly test, functional verification, mold manufacturing.
- Aviation, aerospace: direct manufacturing of special parts, impeller, turbine, blade trial, engine trial, assembly test.
- Light industry: the rapid design of various product design, verification, assembly, marketing, toys, footwear molds.
- Medical: medical device design, trial production, trial, CT scanning information of the physical, surgical simulation, the preparation of human bone and joint.
*National defense: the design, assembly, trial production of special weapons components, the direct production of special parts, and the production of remote sensing information.
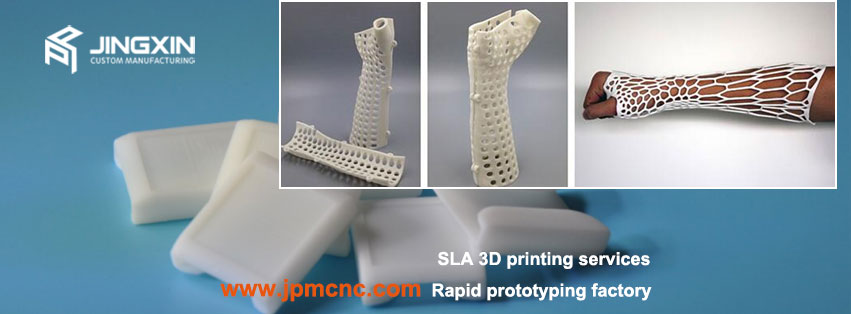
3D printing services, SLA prototype service, rapid prototypes, SLA 3D PRINTING
*Precision casting: The liquid resin used in the photo-curing Rapid prototyping equipment is composed of carbon, hydrogen, oxygen and other elements of the polymer material. At 700 ℃ above the temperature, can be completely ablated, there is no residual material. For the loss Wax manufacturing precision casting model, this is a very important performance. At present in the jewelry industry can replace the artificial carved wax process, can greatly improve the molding accuracy and efficiency.
Selective laser sintering (SLS)
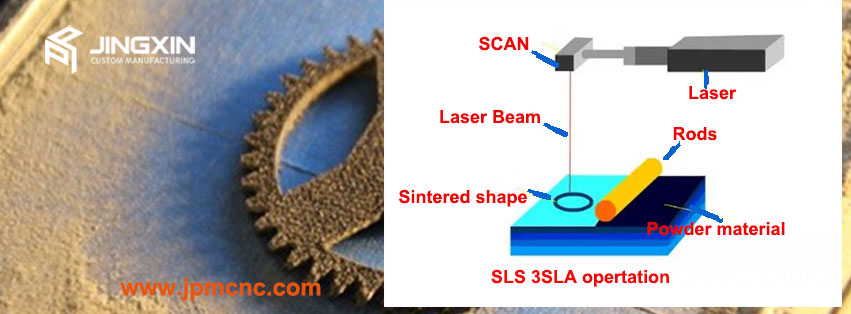
SLS 3d printing technology
1.Overview and process
Selective laser sintering (SLS) was developed and patented by Dr. Carl Deckard and academic adviser, Dr. Joe Beaman at the University of Texas at Austin in the mid-1980s. Selective laser sintering (SLS) is an additive manufacturing (AM) technique that uses a laser as the power source to sinter powdered material. SLS is a very high precision 3d printing process, the use of materials is powder material(typically nylon/polyamide ), thermoplastic, metal powder, ceramic powder. Laser in the computer under the control of the powder scanning to achieve the material sintering bonding.
2.SLS Technology
First, the CAD model of the sample to be prepared on the computer. Then processed by the hierarchical software to obtain the data information of each processing level. When forming, set the preheating temperature, laser power, scanning speed, scanning path, single layer thickness and other process conditions. First on the table with a roll of powder material, the CO2 laser emitted by the laser beam in the computer Under the control.
The powder layer is selectively scanned according to the CAD data of the cross-sections of the layers of the geometrical shapes. At the position of the laser irradiation, the powder material is sintered together and the powder not irradiated with laser light is still loose. And the next layer of powder support; a layer of sintering is completed. The table down the height of a section of the layer, and then the next layer of powder, sintering, a new layer and the former layer of natural sintering together. All sintering Upon completion, the excess powder which has not been sintered is removed and the sample to be prepared.
3.Raw material SLS
SLS material is a key of the development of SLS technology. It plays a decisive role in the forming speed and precision of the sintered parts and its physical and mechanical properties, which directly affects the application of sintered parts and the competitiveness of SLS technology and other rapid prototyping technologies. There is a variety of laser sintered materials developed, according to the nature of the material can be divided into the following categories: metal-based powder materials, ceramic-based powder material, coated sand, polymer-based powder materials.
A.the metal base powder material
There are two main categories of metal-based powder materials, one is a metal powder with a binder as a binder, including a coated metal powder (such as RapidSteel 2.0 of DTM) prepared by coating a metal powder with an organic polymer and Metal and organic polymer mixed powder. In the process of laser sintering, the metal particles are bonded together by the organic polymer to form parts, the raw material after high-temperature removal of the organic polymer, copper, and other post-processing, can be made dense Of metal parts and metal molds. The other is free of organic binder metal powder, such metal powder can be used directly high-power laser sintering into a high density of functional metal parts and mold.
B.Ceramic material
The ceramic material has a high sintering temperature and is difficult to form directly with laser sintering. Therefore, the ceramic-based powder material for the SLS process is a ceramic powder with a binder. In the laser sintering process, the ceramic powder is bonded together by a molten adhesive to form a certain shape and then subjected to a post-treatment to obtain sufficient strength. Commonly used adhesives are the following three categories:
① organic binder, such as polymethyl methacrylate (PMMA), PMMA coated with Al2O3, ZrO2, SiC and other ceramic powder material, after laser sintering forming, and then after degreasing and high-temperature sintering and other post-processing can be quickly manufactured Precision casting ceramic shell and engineering ceramic parts;
② inorganic binder, such as dihydrogen phosphate, NH4HZPO4 melted and decomposed at sintering to produce P2O5, P2O5 reacts with ceramic matrix Al2O3 to produce AlPO4. AlPO4 is an inorganic binder, which can bond ceramic powder Together;
③ metal adhesives, such as aluminum powder, in the sintering process of aluminum melting, melting aluminum can be Al2O3: powder bonded together, while a part of the aluminum will be in the laser sintering process oxidation, the formation of Al2O3, and release A lot of heat, to promote Al2O3 melting, bonding.
4.SLS Advantages & Disadvantages:
The advantages of SLS
(1) More types of raw materials available for SLS. As long as the powder material in the heating viscosity is low, it can be used. Product or model printed by SLS can meet a variety of needs. Compared with other technologies, SLS technology can make metal prototypes or molds, so it has a broad application prospects.
(2) The process is simple. As the technology can use powder materials as raw materials, through laser sintering, can quickly produce a complex structure of the product prototype or mold, so the application of industrial products in a wide range of applications.
(3) High accuracy. Accuracy is affected by the type of powder material, the size of the powder particles, the geometry of the model, and so on. In general, its accuracy can reach between 0.05mm and 2.5mm.
(4 No need to support the structure like SLA printing. In the process of sintering layers, no sintered powder can support the suspended layer.
(5) Material use. SLS technology can be close to 100% of the material probability, because it does not need to support the structure, do not need the substrate support, and the lower price of powder materials, so the cost of modeling is low.
(6)Small deformation to the parts.the workpiece printed by SLS warping deformation is small, do not even need to correct the prototype.
SLS Disadvantages:
(1) long working hours. It takes about 2 hours before processing to heat the powder material near the bond melting point. After processing, it takes about 5-10 hours to remove the prototype part from the inside of the powder cylinder until the workpiece is cooled.
(2) post-processing is more complex. the process of SLS is by heating and melting powder material, to achieve layer by layer bonding, so the surface of the workpiece showing a granular, then the parts need for a certain post-processing.
(3) Sintering process will produce odor. Polymer powder materials in the heating, melting and other processes, the general will be issued a smell.
(4) Equipment prices higher. In order to protect the safety of the process, in the processing room which is full of nitrogen, so it improves the equipment costs.
5.SLS 3D printing Application
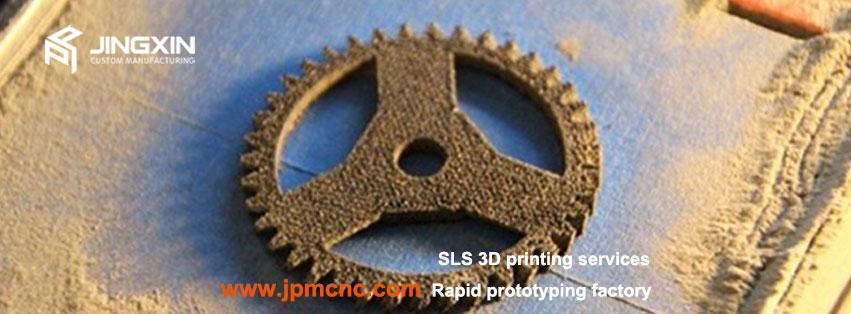
SLA 3d printing prototypes for car parts
3D printing SLS technology in the application of the car
- For the design of verification, performance testing of hand samples (prototype) production.
- For the production of complex parts of the direct production, you can directly installed in the real car running
- The third aspect is for the production of lightweight components on the car, this structural parts used in the car is not a lot, the need for car designers, innovative ideas from the design, with a variety of honeycomb structure to replace the Solid or solid structure.
- For the customization of special tooling and testing equipment.
It can be said today that in the industrial design gradually progress and modeling software tidy ,3d printing for complex modeling production and personalized customization and polymer materials processing has an immeasurable space, 3d printing is still fast Development in the 21st century, in the generation of designers and manufacturers of efforts, I believe 3d print really can completely change the world.
At JINGXIN precision machinery ltd, we’ve specialized in SLS,SLA 3D printing rapid prototyping, custom Rapid machining service, and custom CNC machined parts in China. We have 50 sets SLA SLS 3d printing machines imported from the USA. Additionally, we’ve expanded into several related areas of custom manufacturing, including plastic injection molding and mold design, reverse engineering.
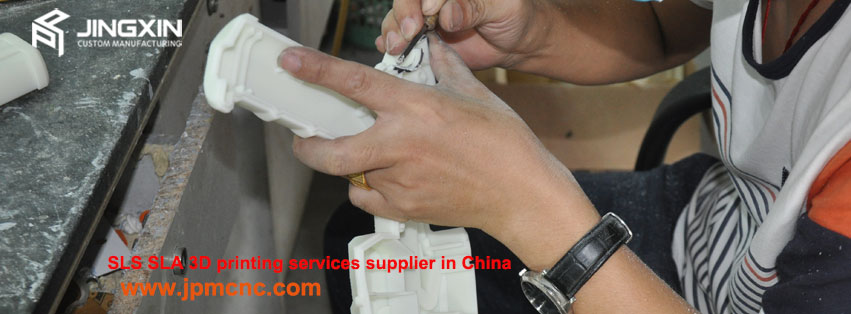
SLA-3d-printing-service-companies-in-China
Having satisfied a vast range of clients across the industrial sector over the past 10+ years, we understand the importance of delivering goods on time and exactly take care about every the customer’s specifications. At JINGXIN, As a rapid prototyping companies in China, we reply the customers’questions in hours and quote the enquiring in 12 hours.
Furthermore, our reverse engineering and rapid prototyping service allow us to customize parts for your project at one-site from developing, pre-production to mass production. Visit our website for more information on our capabilities or send us inquiry at email enquiry@jpmcnc.com