Plastic molding manufacturing & Jingxin LIMITED
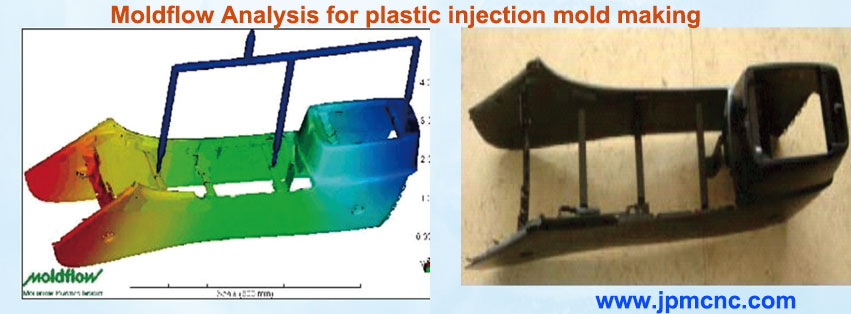
Mold flow analysis can improve plastic injection mold design and making, The best way to detect plastic mould design, save time and cost of mould making
What is the purpose of mold flow analysis? Where does it value?
Moldflow is an essential element of any injection molding design project.The best methods for checking mold design and plastic molding manufacturing.
- Mold flow analysis Can help mold designer knows whether the injected parts are fulfilled into the cavities. It can also provide other useful information, such as injection pressure and clamping pressure required. Before go ahead with mold making and plastic molding manufacturing.
- The mold flow analysis will indicate if the parts have filling problems to the mold cavity. Such as short shots, bubbles, and unbalanced filling, can be determined by mold flowing analysis of the filling curve. The mold-flow analysis allows you to change the plastic injection gate position, injection speed and other processing conditions. You can know whether these problems can be improved or corrected.
- You Can predict the deformation of parts through mold flow analysis. Deformation prediction can be used to compare the gate position, wall thickness changes or design changes.
- Mold flow analysis Can check and correct the problem of the plastic injection molding manufacturing. The best way to detect problems with plastic molds is to mold flow analysis on the computer to make a ‘short shot’. Then it will show the results of which changes are effective and faster.
- Mold flow analysis Can check the efficiency of cooling water circuit. Adding cooling analysis to the deformation analysis can increase analysis accuracy to mold. Because the cooling waterway is the important system to a plastic injection mould. It is hard to modify once it is done, so this kind of analysis is useful before you make the mold.
- Adjust and improve mold weld line. Mold flow analysis predicts where the weld line occurs and helps to move it where it is less prone to problems. It can also provide clues that affect the quality of the weld line. Such as the temperature at which the melt flow front meets and the pressure required to fill the weld line. However, mold flow analysis can not predict the strength of the weld line and its visibility.
Before tooling production begins and plastic molding manufacturing. At JINGXIN, we use Moldflow software to analyze the proposed mold design. And ensure that the mold will be capable of producing the strongest, most uniform parts from each cavity.
Learn more about JINGXIN plastic molding manufacturing and export mould services. Please visit our website plastic injection mold, or talk to our project manager Mr.Sammy Tang for your new project via email enquiry@jpmcnc.com
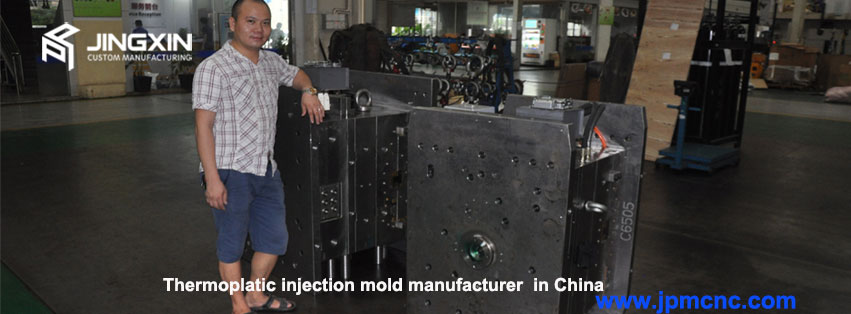
Mold flow analysis can improve plastic injection mold design and making, The best way to detect plastic mould design, save time and cost of mould making