All cnc machining manufacturers try their best to control waste material and excess material in cnc machining process. Because they clearly understand that these waste material and excess material usage means their profit becomes more thinner. Especially for some high precision and complex and intricate high hardness components, its material cost is very high, and having a long machining time and high labor cost. If this kind of material is wasted excessly in cnc machining process, manufacturer’s profit will more thinner. So how to reduce waste in cnc machining processes ?This is involved of CNC Machining Cost Optimization.They are always explore its profoundly and expect to some good solutions to overcome their difficulty.
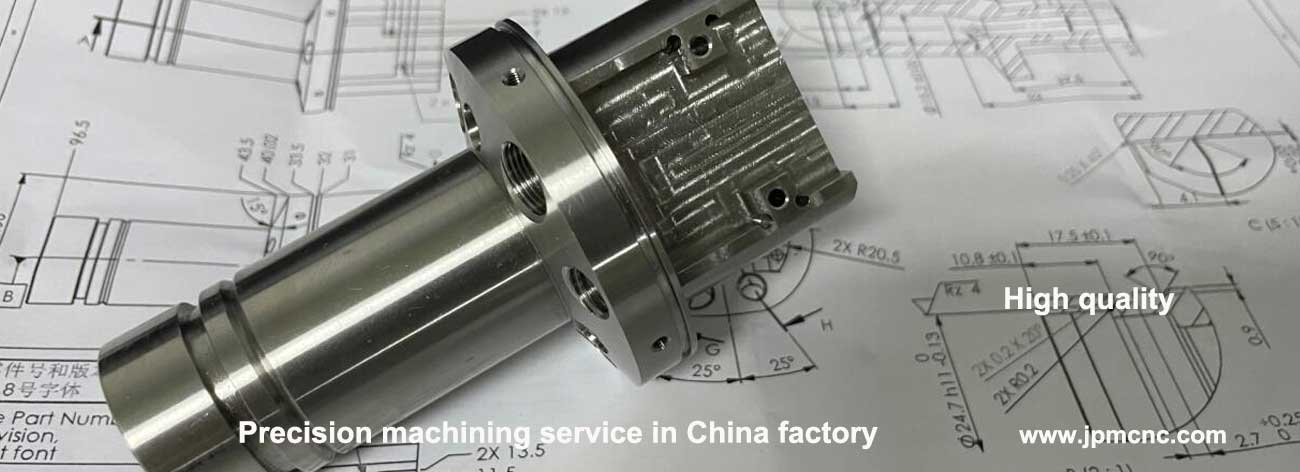
Reduce Waste in CNC Machining Processes
In order to Reducing waste in CNC machining processes and improving efficiency, reducing costs, and minimizing environmental impact. JingXin Experts suggest everyone that some effective approches to achieve this.
Optimize Material Utilization
Checking own raw material in stock, selecting appropriately sized raw materials to minimize excess. Optimize the layout of parts when cutting multiple components from a single block, choose reasonable tolerance cnc machining equipment, shape the parts at one stop as much as possible. Employ well-experienced technician, and Use software to simulate and refine tool paths, reducing unnecessary material removal.
Make Detail Process Planning
For wanted machined parts, we firstly edit process program in accordance with the drawing of custom part and implement a good visual simulation with CAD and CAM soft, then Conduct detailed design reviews to ensure accurate machining. Doing Manufacturability (DFM) access, Create parts that are easier to machine with minimal waste. Use appropriate tolerances to prevent excessive machining. Implement clear, standardized procedures to reduce setup and operation errors. Create real prototypes and inspect its functionality and dimensions and tolerances, if modification is necessary, do it until a qualified sample is finished. In subject to the first sample standard, finish mass production.
Improve Tooling Efficiency
Regularly inspect and maintain tools to ensure sharpness and precision, reducing material waste from poor cuts. Use high-efficiency toolpaths, directly importing CAD files into CAM system,convert into G-code program language avoid manual setting toolpaths, possible reduce process errors occur.
Reduce Cutting Fluid and Coolant Waste
Employ Minimal Quantity Lubrication to reduce the amount of cutting fluid used and saving coolant and lubrication cost to machine. We also Install filtration and recycling systems for cutting fluids and coolants. Meanwhile, the cnc machining process should be ensure that it keeps a safe and stable running.
Implement Automation and IoT Solutions
Monitor performance in real-time to detect inefficiencies or errors early during cnc machining process. Installing sensitive sensor and alert setting on the machine, real-time monitoring each cnc machining action. Once any error and deviation in machining accuracy, System will send message or flashing red light to notice operator to have a modification and adjustment right away. In another one, Automate repetitive tasks to reduce human error and material waste.
Recycle and Reuse Waste
Collect and recycle metal chips and scrap materials. Reuse filtered cutting fluids and minimize disposal.
Regular Employee Training
Train staff on best practices in machining, tool handling, and waste reduction strategies.
Operation of cnc machining in site: Guide staff how to edit operation program, focus on CAD files imported to CAM system, and convert into G-code, avoid manual setting toolpaths and reduce process errors and defect parts occur.
Removing quickly waste material on the machine: When the machine begin processing the part, plenty waste material is produced by cutting, There waste material cut should be removed at once so that cutting move towards toolingpaths smoothly.
Optimization of material usage: Optimize the layout of parts when cutting multiple components from a single block, choose reasonable tolerance cnc machining equipment, shape the parts at one stop as much as possible.
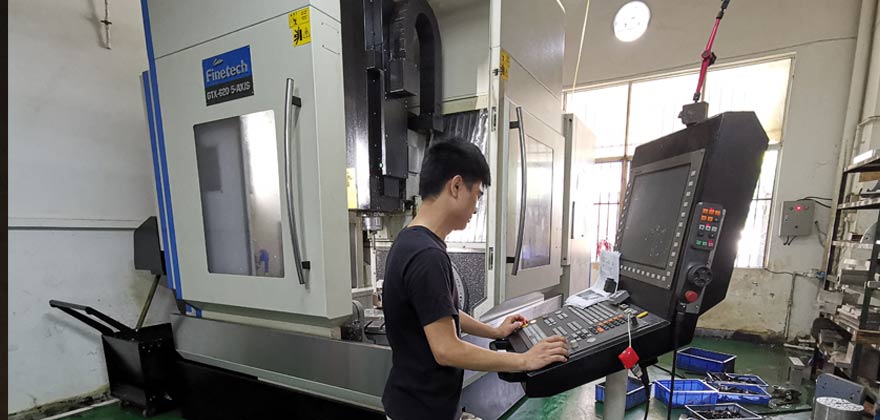
practical operation that convert CAD files into G-code language
Conclusion
How to reduce waste in cnc machining processes ? Complying with the above key methods, we will can reduce the waste cost of cnc machining largely. This is an integration task for improving cnc machining process, from material usage, toolingpaths perfection , lubrication and coolant improvement to employee training, each strategy all shorter the cost of cnc machining. In fierce competitive cnc machining industry, optimizing the cost of cnc machining process can make manufacturers to gain more much profits. These beneficiaries can have more capability to contribute the welfare issues in modern society.