CNC Machining have become more popular in manufacturing process industry due to its flexible design, precision process and automation operation. In many industries, more and more complete and intricate mechanical components, functional parts and structural parts request being machined in high precision. This makes cnc machining must play a pivotal role in manufacturing process. Especially such as automotive sector, aerospace and medical industries. Today Let us learn that how cnc machining works.
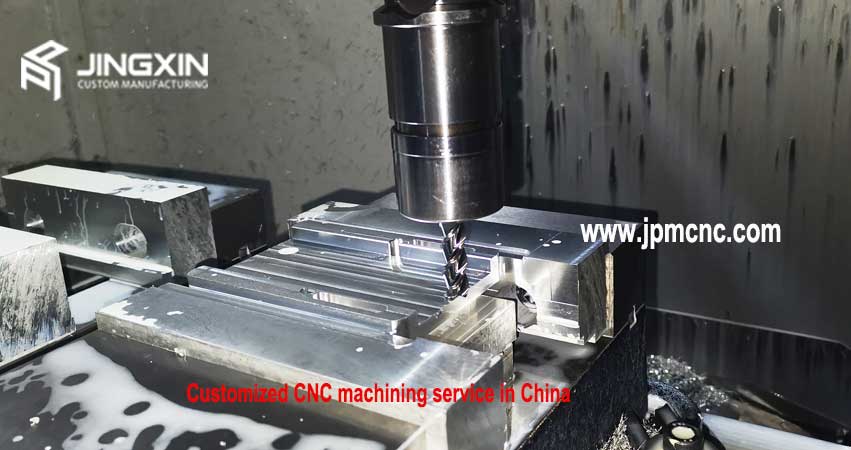
Custom CNC machining Process
Definition Of CNC Machining
CNC (Computer Numerical Control) machining is a precision manufacturing process that uses Computer-Aided Manufacturing (CAM) software to control the movement of tools to process parts and machinery. It allows for precise production of complex parts by automating the machining process. CNC Machining contains several kinds of process options, including of cnc turning machining, cnc milling machining, cnc grinding machining,cnc router machining and cnc EDM machining etc. With the rapid development of tech and science, CNC machining had been widely used in industries such as aerospace, automotive, medical, and consumer electronics.
How to operate a CNC machine step by step?
We need understand how cnc machining works and help us to operate a cnc machine step by step. The CNC machining process involves several steps, from initial design to the finished product. How do we operate a cnc machine rightly ? The below guideline will indicate you step by step.
Designing the CAD Model
From the beginning, Our engineers often use Computer-Aided Design (CAD) software to create a digital model of the part, which includes detailed specifications, such as dimensions, geometries, and tolerances. Then saving the CAD file on the computer.
Converting to CAM Program
Engineers will export The CAD file from their computer, and import into Computer-Aided Manufacturing (CAM) software for implementing cnc machining move paths. CAM software generates a toolpath, which dictates the movement of the cutting tool. The program translates the design into G-code, the language understood by CNC machines, and executes the pre-programmed cnc machining.
Machine Setup
In accordance with different machined material block, we will set up machine speed and clamping tools and ensure securing to the machine bed or a work-holding device. Of course we also should choose correctly Tools, such as drills, mills, or lathes, are installed based on the operations required.
Execution of Machining
The CNC machine executes the G-code instructions, guiding the cutting tool to shape the material. The CNC Machining Process may be Common machining operations as follow.
Milling: Rotating cutting tools remove material from the workpiece.
Turning: The workpiece rotates while a stationary cutting tool shapes it.
Drilling: Creating precise holes in the material.
Grinding: Achieving fine finishes and tight tolerances.
We will choose appropriate machining method to finish execution of machining
Quality Inspection And Improvement
The execution of machining is over, the part is inspected for accuracy using tools like calipers, micrometers, or Coordinate Measuring Machines (CMMs). These inspection instruments are indispensable for cnc machining manufacturer. When we find some imperfections and deviations on the workpiece, we will have a reasonable adjustment and correct the program to process qualified components.
Applications of CNC Machining
- Aerospace: High-precision parts for engines, structural components, and avionics.
- Automotive: Engine components, custom parts, and tooling.
- Medical: Surgical instruments, implants, and diagnostic equipment.
- Electronics: Housings, connectors, and precision components.
Solutions for Common CNC Machining Problems
Q1. What method to improve that Tools is Wear out and Breakage During CNC Machining ?
A1: Tools wear out or break due to excessive cutting forces or improper use. Use appropriate cutting parameters, such as feed rate and spindle speed. Regularly inspect and replace tools as needed.
Q2. How to Treat The Dimensional Inaccuracies Of Machined parts ?
A2: Parts may not meet specified tolerances due to thermal expansion, machine calibration issues, or tool deflection. Calibrate the machine regularly and use precision tools. We can optimize cutting strategies to minimize tool deflection and compensate for thermal effects.
Q3. How to improve Poor Surface Finish of machined parts ?
A3: The machined part has rough or uneven surfaces.This may be the reason that you use improper operation and wear out cutting tools. We should use sharp tools and appropriate cutting speeds. Additionally adding coolants to reduce heat and vibration during machining.
Q4. How to resolve this problem like Material Deformation ?
A4: Thin or flexible materials may deform under cutting forces. We can use proper clamping techniques and adjust the feed rate to reduce stress on the material.
Q5. How Will We Prevent Machine Downtime During CNC Machining ?
A5: Unexpected breakdowns lead to production delays. Such as electricity stop and machine maintenance. We may implement a preventive maintenance schedule and keep spare parts readily available. If necessary, we can have shift work to saving production time.
Q6. What solution is For Enough Chips accumulated interferes with the cutting process?
A6: Fixing additional cooled system and using cutting fluid to flush chips away and select tools designed for effective chip evacuation when chips accumulated enough to impact with cnc machining operation.
Q7. What shall we do If Programming Errors is occurred during cnc machining ?
A7: Incorrect G-code leads to machining errors. In order to prevent programming error from cnc machining and avoid problem like this,we should verify the program using simulation software before running it on the machine.
Q8. What Solution is Adopted for Machines Vibration During Operation?
A8: Excessive vibration causes poor finishes and tool wear. rigidly impact the precision and quality of machined parts. We should optimize machine settings, use dampened tools, and ensure the machine and workpiece are properly secured.
Conclusion
From the above description, we found CNC machining had been regarded as cornerstone of modern manufacturing, combining automation, precision, and versatility to create high-quality parts. By understanding how CNC machining works, manufacturers can leverage its capabilities to produce high quality components efficiently and consistently, meeting the demands of today’s competitive industries.