As professional cnc machining manufacturers, who always purchase for best cost of cnc machining while they are processing high precision parts. It is beneficial to make more money for manufacturers and exceed their competitor in the present fierce competitive market. So they also take their ideas to optimize cnc machining cost consistently. Therefore, optimizing CNC machining costs involves a combination of design, material selection, process planning, and operational efficiency. Passing decades years practical experience, We summarize the below top 8 cnc machining cost optimization strategies.
1. Optimize Part Design
Part design involves of geometry shape, internal structural design, surface finish of the part and intricate details that increase machining time and tool wear. We focus on cnc machining, take a consideration of how to optimize the process to reduce its cost. Applying tight tolerances in cnc machining only where absolutely necessary,regardless of unnecessarily stringent tolerances. Minimize setups is necessary, design parts for easy clamping and fixturing to reduce the number of setups required. Avoid features requiring special tools or multi-axis machining unless critical.
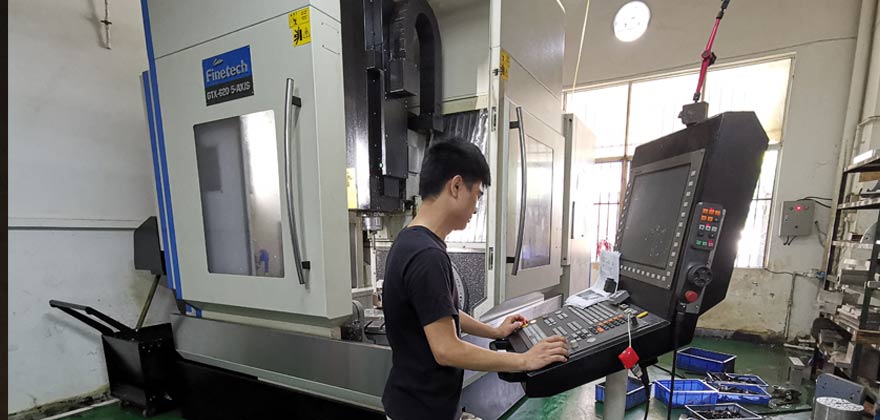
cnc machining design optimization
2. Select Cost-Effective Materials
We can choose some easily machinable materials like aluminum (e.g., 6061 or 7075) or brass that are easier to machine compared to harder materials like stainless steel or titanium,if the parts functionality and applications is allowable. Caculating the quantity of finished products from the cutting of raw material, eliminating waste material and reusing waste waste material as soon as possible.
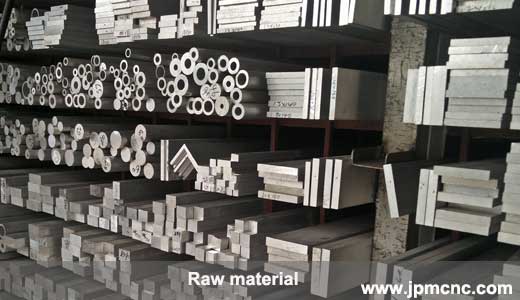
Selection cost-efficiency material
3. Optimize Tool Paths
In technique improvement, We employ talented operators to collaborate to work with well-experienced engineers and handle and choose High-Efficiency Machining (HEM). By modern CAM software to program efficient tool paths that reduce machining time and tool wear. We optimize roughing strategies to remove material quickly and safely. Reduce tool travel and retraction where possible.
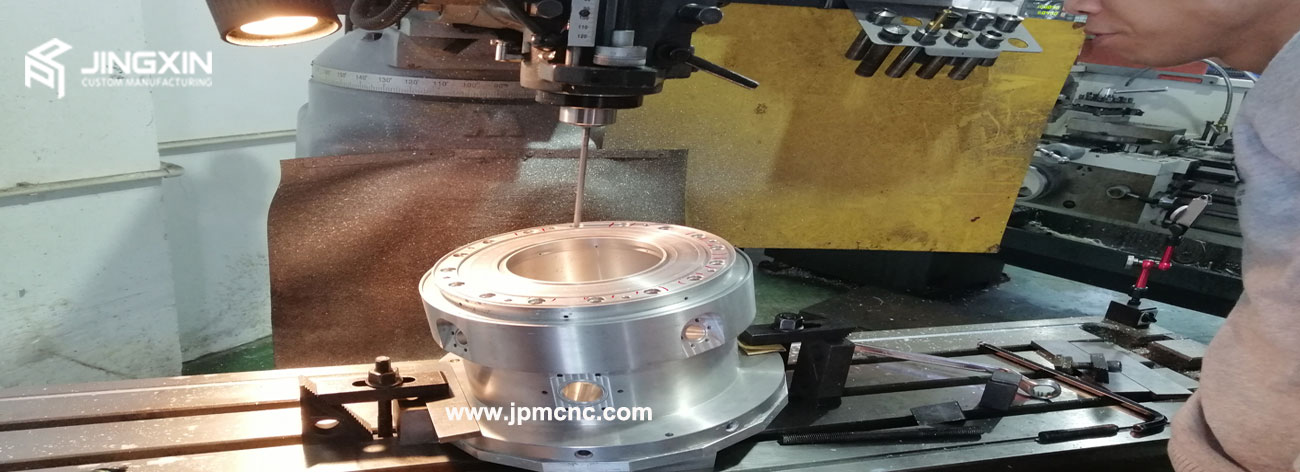
Optimize tool paths
4. Reduce Average Part Process Cost
The method means that we suggest client to increase the quantity of the order as soon as possilbe. The Higher volume of parts , the lower cnc machining cost, The cheaper finished product price that provided to customer. Let us take a good example to explain it. Such as , There is a significant difference between the price of 50 sets and 100 sets of the order. Supposed Our material cost is 15 usd/set, Our cnc machining cost is 20 usd/hour, which includes of CAM program edit, machine adjustment, testing cost and mass production cost, additionally our profit rate is 20%. Predicting each part production time is 2 hour, machine adjustment time and CAM program edit needs spend 24 hour, if 50 sets order, its price is 77.52 usd per one, but 100 sets, its price is 71.76 usd. This is an effective approche for reducing cnc machining cost.
5. Improve Operational Efficiency
JingXing Technology Company introduces robotic arms for loading/unloading to reduce labor costs. Regular maintenance ensures the machine operates efficiently and minimizes unexpected downtime. We are known of factors of cnc precise machining and manufacturing deviation, always improve consistently cnc machining precision in numerious practical operations.If necessary, we have frequency regular machine operation training courses.
6. Outsource Strategically
We have a measured supply chains and work with CNC service providers with expertise in your specific type of machining. For some simply and common process part, we can outsource them to our faith sub-supplier who cooperate with us for a long time. Doing this way, larger production runs can reduce unit costs through economies of scale.
7. Post-Processing Cost Management
After cnc machining, parts require minimal deburring, finishing, or polishing. Consider machines capable of combining milling, turning, and drilling in one setup. Reduce machines shift and saving more labor cost and lead time. We select more advanced integrated cnc machining equipment.
8. Analyze Production Workflow,Make Rigid Quality Control System
Our factory ensures seamless communication between design, programming, and manufacturing teams to avoid costly revisions.Strictly excuse check-self actions irregularly during mass production and ensuring machined parts achieve qualified level and tight tolerance. This will avoid some defects and operational errors occurred. We implement international quality system rigidly such as ISO 9001 2015 and IATF 14969 international standard.
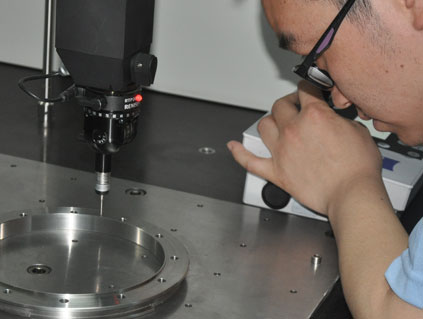
Check-self quality control during cnc machine
In summary, The above top 8 cnc machining cost optimization strategies can reduce cnc machining cost of the part in effective. Complying with these keys points during CNC machining, not only lower the overall cost of the machined part , but also guarantee that factory can produce high quality machined parts.
At JINGXIN ®, We offer CNC machining services with plastic and metal parts for Short-run production or 10000+ production. Applications include parts for Auto parts, Medical, Industry. Typical tolerance range from +/- 0.01mm-0.05mm; The Fast lead time within3-6 working days.
ISO certificated Factory in China Advanced and high-speed HAAS US brand CNC machines
Skilled R&D Team+Sales Team Manufacturing solution for your projects
Welcome to Contact our Project manager (Mr. Sammy: enquiry@jpmcnc.com) directly for your project.